Tecnologie di decarbonizzazione
La sfida posta dalla necessità di un futuro sostenibile e dalla transizione energetica richiede uno sforzo massiccio e una strategia globale.
Mentre molti sforzi mirano ad alimentare la produzione solo con energia verde, aumentare l'efficienza energetica dei processi esistenti è il primo passo per ottenere guadagni in termini di sostenibilità.
Saipem continua a perseguire obiettivi relativi alla gas monetisation, ai relativi processi di decarbonizzazione e di evoluzione della transizione energetica, con un focus sul consolidamento e sviluppo dei processi e delle tecnologie.
Sebbene le energie rinnovabili cresceranno velocemente, il settore Oil&Gas coprirà ancora una quota molto importante della domanda energetica nei prossimi decenni.
Per questo è fondamentale progettare nuove configurazioni ibride, in grado di rendere la produzione sempre più sostenibile e ridurre le emissioni di CO2.
Stiamo quindi intraprendendo approcci innovativi per ottimizzare l'integrazione dei concetti di energia rinnovabile e stoccaggio energetico con le operazioni Oil&Gas per la produzione di idrocarburi, sia a terra che a mare.
Supercups
Una tecnologia proprietaria Saipem per l’efficienza energetica negli impianti di urea
La nostra tecnologia proprietaria SuperCups è una soluzione ottimale per risultati immediati in fatto di efficienza energetica e operazioni sostenibili nel settore dei fertilizzanti. Vediamo perché.
I fertilizzanti sono essenziali per coltivare le colture necessarie per nutrire miliardi di persone e svolgono un ruolo cruciale sia nella decarbonizzazione che nella sostenibilità del settore agricolo.
L’urea è uno dei fertilizzanti più diffusi al mondo e consente agli agricoltori di utilizzare un prodotto ricco di azoto per migliorare con costi contenuti le colture agricole, sostenendo al contempo la crescita di tutti i Paesi in via di sviluppo.
L’elemento che lega i concimi alla decarbonizzazione è l’idrogeno da cui essi derivano. I metodi attuali per produrre l’idrogeno si basano su processi ad alta intensità di carbonio come lo steam reforming del metano proveniente da gas naturale o la gassificazione del carbone. Viene quindi convertito in ammoniaca e infine in derivati come l’urea.
In questo caso una buona parte dell’anidride carbonica creata come sottoprodotto della generazione di idrogeno viene riciclata per produrre urea; tuttavia, la quantità di CO2 residua emessa nell’atmosfera è ancora significativa.
Mentre sono in atto molti sforzi per trovare la combinazione più conveniente di tecnologie per ottenere prodotti verdi, oggi sono disponibili comprovate soluzioni per migliorare la sostenibilità della produzione di urea.
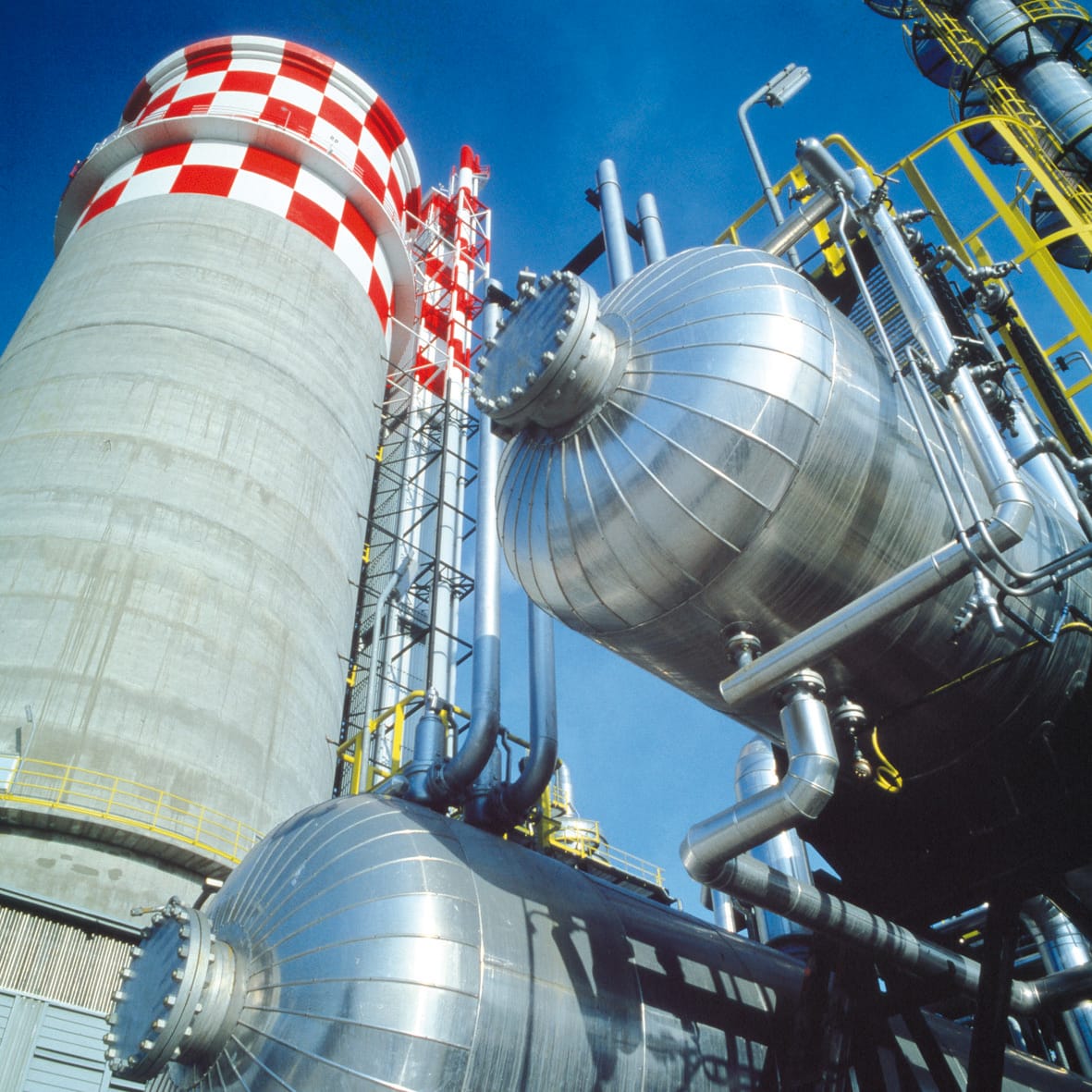
In questo contesto la tecnologia SuperCups rappresenta un’ottima soluzione per migliorare il processo dell’urea al suo interno ottimizzando le prestazioni del reattore di sintesi.
SuperCups rappresenta una risposta diretta alla domanda di processi sempre più performanti, con l’obiettivo di ottimizzare gli investimenti di capitale per le apparecchiature ad alta pressione, ridurre il consumo di energia e ridurre il footprint ambientale della produzione di urea.
SuperCups aumenta l’efficienza di conversione dei reattori a urea incrementando la produzione senza alcuna modifica all’impianto o la riduzione del consumo energetico a parità di capacità produttiva.
Risparmio di carburante significa una riduzione delle emissioni di CO2 senza la necessità di alcun sistema di cattura del carbonio evitando così qualsiasi problema legato allo stoccaggio e all’utilizzo della CO2 catturata.
L’innovazione di SuperCups risiede nella creazione di uno spazio di reazione confinato all’interno della geometria del reattore, ovvero le coppe.
SuperCups è stato testato per la prima volta nel 2016 in collaborazione con l’azienda austriaca Borealis e l’azienda pakistana FFC ed è ora commercializzato da Saipem come apparecchiatura proprietaria per le unità di urea.
La tecnologia è stata efficacemente applicata per progettare una nuova generazione di reattori di urea e per migliorare le prestazioni delle unità esistenti attraverso retrofit di progettazione.
L’innovazione di SuperCups è stata implementata in diversi progetti che contribuiscono a benefici ambientali come la riduzione dell’intensità di carbonio degli impianti di urea e la riduzione delle emissioni equivalenti di CO2.
Tra i risultati
Il case study è rilevante per l’ammodernamento di un reattore per la produzione urea per un cliente indiano che gestisce un impianto di dimensioni medio-piccole.
Per dare un’idea semplice, ma efficace, dell’importanza di tali contributi, basti pensare che la citata riduzione dell’intensità di carbonio della produzione di urea è stimata essere equivalente alle emissioni di gas serra di circa 3.000 autovetture. 3.000 automobili tolte dalla circolazione in un solo colpo!
L'urea diventa digitale
Realtà virtuale per ottimizzare la produzione di urea nel mondo reale
Un ulteriore sforzo in questo contesto è rappresentato dall’accordo siglato con Honeywell per lo sviluppo del prodotto e la commercializzazione di un “Digital Twin” nell’ambito della tecnologia Snamprogetti™ Urea di Saipem.
La soluzione è in via di sviluppo su Honeywell Forge, il software di gestione delle prestazioni aziendali di Honeywell, per consentire ai clienti di migliorare la produzione di urea tramite la simulazione virtuale dei processi chiave.
Il nuovo servizio sarà commercializzato con il nostro marchio e supportato da Honeywell Forge.
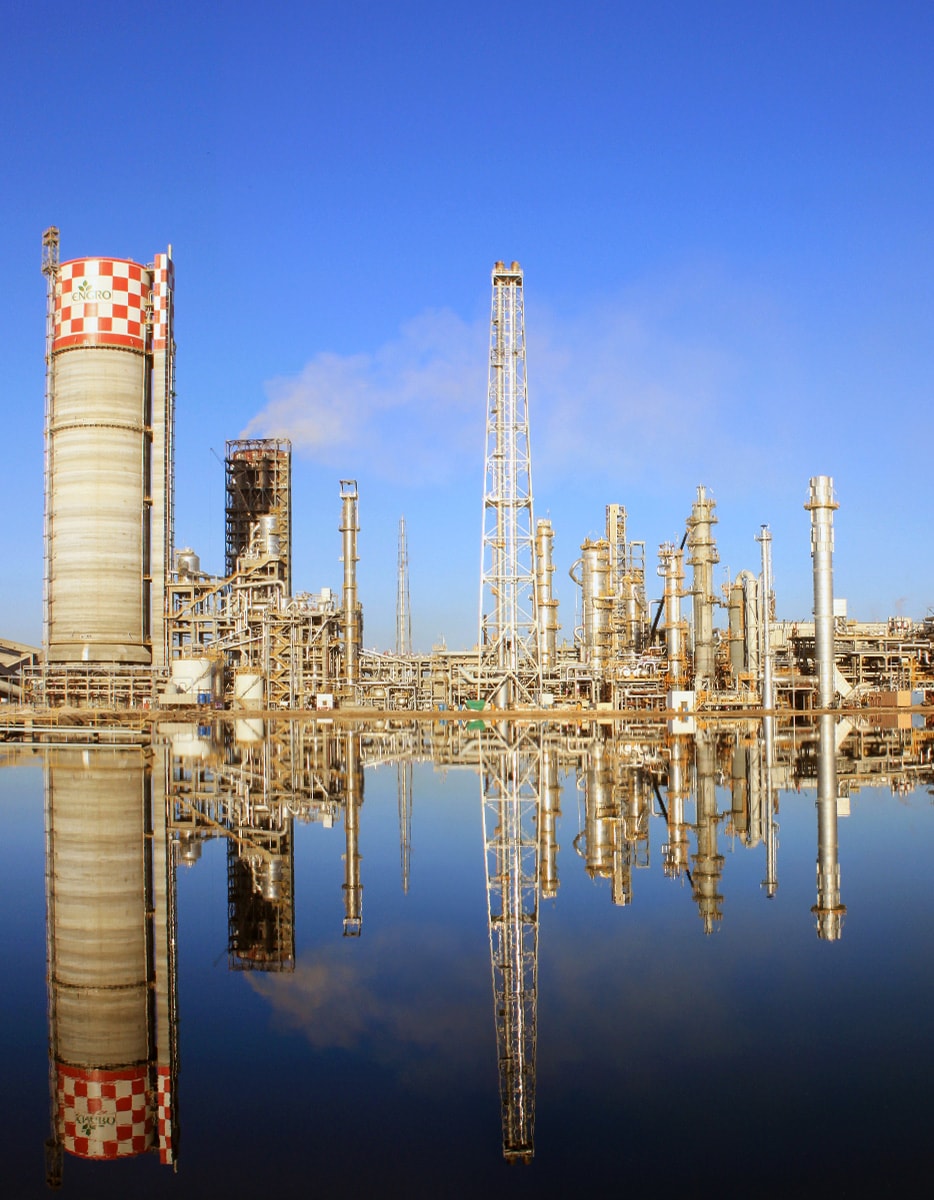
Saremo responsabili della gestione e del supporto tecnico dello strumento digitale, coinvolgendo Honeywell quando richiesto.
La soluzione digital twin di Honeywell sarà utilizzata anche come modello virtuale per guidare gli ingegneri con informazioni utili sulle prestazioni della macchina e sulle esigenze di manutenzione al fine di ottimizzare la produzione di urea.
Con la soluzione Honeywell Forge, implementata in oltre 60 unità di processo in tutto il mondo, potremo fornire risposte in tempo reale sulla gestione operativa degli impianti, raccogliere dati per il monitoraggio e la manutenzione predittiva, contribuire all’ottimizzazione delle operazioni dei nostri clienti e fornire maggiore valore agli stakeholder.
La soluzione ci consentirà di rimanere in stretto contatto con i nostri clienti, anche dopo la consegna dell’impianto, di modernizzare l’offerta come licenziante e di raccogliere feedback sulle prestazioni dell’impianto.